SIX HUNDRED MILLION REASONS FOR A PAL LINE
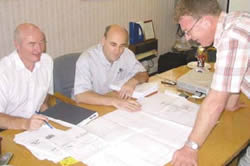
(Left to right) John Adamson and Mark Heron of Decorpart
pore over the plans for the new line with PAL’s Tony Evans |
PAL Europe has received an order from Decorpart of Nelson, Lancashire
for a fully automatic anodising line. The line is described by PAL
Europe’s Managing Director, Bruce Norsworthy as having a "huge output"
for anodising pharmaceutical cans, and ferrules for the production
of nebulisers. It will also have the capability to anodise dispenser
shrouds and actuator covers for perfume bottles and dispensers for
creams.
"And when I say ‘huge output?I really mean it," he says. "The
machine will be processing, for starters, a staggering 600,000,000
pieces every year! There are almost certainly examples of Decorpart’s
work in your bathroom or on a dressing table in your home."
Decorpart is the world’s largest independent producer of its specialist
component products and supply the world’s leading pharmaceutical,
cosmetic and perfumery markets," explains Mark Heron of Decorpart.
"Dispenser shrouds and actuator covers are one of the fastest growing
sectors globally. The dispenser market has developed rapidly due
to the increasing importance placed on skincare and personal hygiene.
We remain focused on being at the leading edge of design by working
on new ideas for ‘encapsulating?the dispenser and adding that all
important finishing touch of creativity. Whether a perfume bottle
or dispenser for cream, our products are designed to add both functionality
and aesthetics.
"The tremendous growth and importance of the pharmaceutical industry
has created challenges for all suppliers when it comes to the integrity
of packaging. We have embraced this opportunity and developed as
the major European manufacturer of pharmaceutical ferrules and cans.
We’ve both created and enhanced primary packaging for active substances
and formulations. As you can imagine a rigorous quality assurance
system ensure compliance with product and regulatory standards.
"At Decorpart we place great importance in products that manage,
and come into contact with, patient dosage. Our anodising process
is designed to create a suitably superior protective barrier, with
very stable formulation, a high breakage-protection factor, and
a chemically tight barrier.
"Our expansion plan takes into consideration the fact that an increasing
number of drugs will be administered using nebulisers in the coming
years.
"Technology plays an ever-increasing role in the maximisation of
quality and value and we are constantly investing in new technology
to stay head of the pack. Our investment extends to include a ?million
new purpose-built pharmaceutical production facility, which, by
releasing existing capacity will effectively also double our capacity
in both the dispensers and cosmetic sectors of the business. Our
new PAL machine will be housed within this new pharmaceutical building.
"There were several reasons that we opted for a PAL line. We wanted
a new concept and not just another anodising line. We felt that
with PAL’s background in electronics, their understanding of the
needs of this line for pharmaceutical products was very good. We
reviewed reference sites and were impressed with the quality of
the lines already supplied. In addition, and very importantly, the
value for money offered was very competitive."
The machine comprises a complex arrangement of the actual main
35 metre long, 6.3 metre wide, and 5.5 metre high, Anodising line,
a similar length parallel storage line, with loading and unloading
shuttles that move the flight bars in and out of the Anodising line.
An automatic jigging machine feeds, and loads, the individual trays
that hold the parts. The operator then manually loads these filled
trays onto the cassettes. Each cassette can hold up to 3300 parts,
and each flight bar holds three cassettes. A shuttle mechanism automatically
brings the flight bars to the load positions, of which there are
ten. Similarly the unload shuttle takes the completed work to a
similar number of work stations for unloading the parts. As these
parts must not be mixed, strict rules apply to the relationship
between the loading and unloading positions. Each flight bar is
tagged to ensure correct disposition in the line and traceability.
The unload area is also in a clean- room, so the passage of the
shuttles and the storage line transporters in and out of that area
presents an interesting engineering challenge.
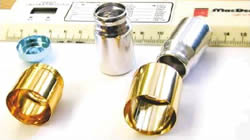
Just five of the six hundred million parts that will be put
through the PAL line |
Due to the requirements of pharmaceutical validation, any out of
range parameter is flagged up and as the parts are unloaded an indicator
will show the operator that the parts are good, or need a decision
on their acceptability based on the nature of the out of range incident.
The machine will have two dye stages for the parts that need colour
for identification or cosmetic reasons.
A specially designed transporter will handle the work around the
aggressive chemical polish, which runs at over 100oC. Two further
transporters handle the rest of the process, of anodising and seal,
and maybe dye. Drying on line require three gas fired indirect drying
units.
The machine is enclosed to protect the new factory environment
and operators from any fumes and this supplements the lip exhaust
system in place within the body of the line. A novel method of treatment
will be employed to handle the fumes arising from the brightener,
and the level of emission will be far lower than the present standard
of emissions requires. Future space is included in the main line
too, with allowance for further expansion when production needs
determine it.
Further information on Decorpart at www.decorpart.co.uk
|