OSSTjWin: NEW VERSION AVAILABLE
PALCON in Malaysia, the development centre for the
OSSTjWin, PAL’s widely used ordering and monitoring
system, has now been in operation for more than three
years.
The development team has been working hard to release
new versions. Besides minor features, the next version
released this September, contains the following major
features:
- Flashback
This is a very powerful tool enabling the user to re-play the
past 24 hours, in real time or in a higher speed format. All
transporter movements and flightbar locations, with their data,
can be monitored, using the same function that is normally used
during production. The user can explore it like a video/DVD
player and pause, play step-by-step forward/backward with the
selected speed, play forward/ backward in real time or at a
higher, selectable speed. The user can easily search for a certain
time of the day or just move a time ‘slide bar?to the required
time slot.
The advantage of this function is to find the cause of all
sorts of problems, such as when:
- A built-in basic MMI (Man Machine Interface)
This is like a stand-alone software package, fully integrated
in the OSSTjWin. There are two different purposes of this function:
The normal purpose is to customise the screens with the equipment
around the tanks, like filter pumps and sump tanks with their
pumps and valves. The second purpose is, if there is a small
or medium sized waste water treatment for the line, it could
be included in the same control system with obvious cost saving.
Those screens can be designed by PAL engineers, or even by
the customers themselves. There is a basic, but powerful, built-in
editor to design the screens. There are standard symbols like
tanks, pumps, valves etc., where each object can have an associated
"tag" to indicate its status (volume for tanks, different colours
for off/on/alarm status on other objects). Each object can have
a "link screen", when, by clicking on the object, the other
screen is displayed. The users can also create their own symbols,
which can change shape depending on the status of the "tag"
variable
Besides the advantages of customising the screens for the line,
the advantages of this function, when used for a waste water
treatment are:
- Side Equipment Function
This function will collect standard side equipment instruments
for each station and display them on a separate screen. By clicking
on a tank, all associated instruments for this tank like temperature
meters, rectifier meters, switches etc., will be displayed.
- Predict Cycle Scheduler
This new scheduler is based on a fixed cycle (a time/way diagram).
The fixed cycle ensures a high output but with some limitations
in mixing different products. Even though, in a sub-cycle (e.g.
zinc), the time can be individually set on any multiple of cycle
time. For example, if the cycle time is 6 minutes, the zinc
plating time could be set to 6, 12, 18, 24, etc., minutes.
The "Predictive" part is that the user can enter the production
list for the day, select priority for the different orders to
be run, and finally select "Optimise". The system will optimise
the usage of the line in the best way, trying to keep the sub-cycle
(e.g. zinc) as much used as possible, with its different plating
times. The user will also get the information about when each
order will be finished!
Another feature is that the user can enter the production list
for next day, just to see when the different orders will be
finished. And when running with any particular production list,
the user can try to re-optimise it, changing priorities and/or
adding other orders to the production list, to see the impact.
Then the user can select "Go" or cancel this new production
list optimisation. 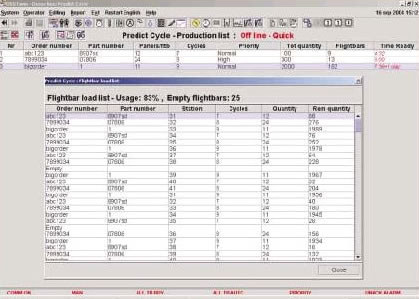
Example of the Predictive Cycle function
|