SURFACE FINISHING ANOTHER SUCCESS STORY FOR PAL
In recent years, thanks in no small part to the establishment of
the PAL Surface Finishing Group, led by Tony Evans, working closely
with PAL’s Surface Finishing consultant Peter Salmon, the company
is building a strong and sound reputation for providing reliable
and robust machines for the surface finishing industries.
Users are plating an incredible range of products as the following
A-Z of products printed in a special Surface Finishing issue of
PAL News in Autumn 2003 show.
Aluminium alloy wheels, aircraft engine parts, automotive industry
requirements, bicycle dynamo lamp sets, bicycle wheels, brass components,
car parts and accessories of all shapes and sizes, coins, door furniture,
exhaust pipes, fasteners galore, gas fittings, handlebars, hardware,
heat sinks, hip joints, medical products, mobile phone antennae,
plumbing fitments, pistons, pump parts, sanitary ware, Sari guards
for motorbikes, silencers (mufflers) for motorbikes, spark plugs,
sun glass frames, supermarket trolleys, valves, welding equipment,
wheel rims for cars and motorbikes, ?. and much, much more!
Some companies such as Honeywell have a foot in both the traditional
electronics and surface finishing worlds, and their story unfolds
here!
RISING TO HONEYWELL’S CHALLENGE
With a manufacture time of just 12 weeks and exacting metal distribution
requirements, Honeywell set PAL a formidable pair of tasks when
ordering a new machine. The new machine was installed in Thailand
and commissioned in August 2003. It is being used to plate heat
spreaders for semiconductor processors produced by several major
chip manufacturers. The heat spreaders are plated with Nickel and
the metal distribution on the parts must be very precise.
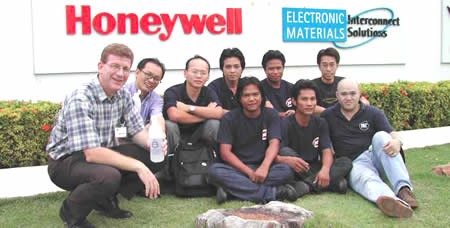
The PAL team relaxing at Honeywell
The new fully enclosed machine has an output of more than one heat
spreader per second, and features a veritable catalogue of PAL’s
state of the art features:
- Two gate-type transporters with drip trays
- Siemens PLC + PROFIBUS
- Variable speed mechanical agitation
- Automatic level control in all process tanks
- Automatic water conservation system in all rinse tanks
- Top spray system in all tanks to wash the flight bars
- PP Anode diaphragm shields and PP shielding system in the plating
tanks
- Sumps for plating tanks
- Automatic dosing
- Automatic dummy plate out system
- MMI control system
- Submerged TI clad anode rails
- Carbon treatment system
- PP containment tray on the structure under all tanks
- Racks that have been specially designed by team of engineers
from PAL, Honeywell and M+B Racks
"There are numerous reasons why Honeywell selected PAL as the supplier
of choice for this line," explains Paul Silinger, Sr. Chemical Engineer
and Project Leader, Honeywell Electronic Materials, Global Operations.
"We have had number of years of a good experience with the company
from our printed circuit board and packaging operations. Further,
we became aware of PAL’s strong presence in Thailand for both service
and spare parts. I have visited several PAL installations in Asia
as a part of our vendor selection process and was very impressed
with the current technology and positive experience of PAL current
customers.
"As a part of Honeywell procurement process, it is always important
to know our vendor’s understanding of our needs and their willingness
to accommodate any special requirements. After meeting with PAL
engineers and visiting their manufacturing facility, we knew we
have the right supplier for this line. The project procurement experience
further confirmed that."
Prasit Bumrungsaksilp, General Manager of Honeywell Electronic
Materials, Thailand is equally enthusiastic. "We are delighted to
work with the PAL team as our business partner in supporting our
growth in Thermal Spreaders business," he said. "The PAL machine
will enhance Honeywell’s plating capability in Southeast Asia and
its flexibility complements other high volume state of the art plating
equipment located here. It demonstrates our continued commitment
to be a worldwide number one supplier of heat spreaders for semiconductor
packages."
"We enjoy rising to challenges; and the combination of achieving
a tight plating distribution guarantee coupled with the speed of
manufacture certainly gave us plenty to get our teeth into," says
Tony Evans of PAL.
"We took a leaf out of the Honeywell book?. their website highlights
their company culture by asking ‘Would you be satisfied without
telephone service for more than four hours a month? How about no
electricity at home for an hour each week? Clearly not. It's no
different with our customers. They want better than 99% problem-free
performance when they buy Honeywell products to use in their airplane
engines, automobiles, computer chips, chemical end products, or
other critical equipment. They also want fresh ideas that help them
build their future??This exactly reflects our culture at PAL and,
like Honeywell we believe it is not good enough to merely satisfy
almost all our customer's expectations; but to exceed all of their
expectations. We greatly enjoyed working with Paul Silinger and
his team on the design of the machine and are confident that they
will not only get ‘better than 99% problem-free performance?but
also have a machine of which they can be justly proud and continuing
input and assistance from us throughout the long life of the machine.
"The machine buy-off was scheduled to take place when the SARS
outbreak was at its height, so I was asked to conduct it on behalf
of Honeywell. It is a tremendous compliment to PAL that a customer
would trust us with such a key task. We always take buy-off extremely
seriously and pore over every millimetre of the machine ensuring
that everything is just as it should be. However I think it is fair
to say that this time I, John Chau, Ronald Yeung, Paul Jew and other
members of the PAL team, went over and over the line, adopting something
of a ‘gamekeeper turned poacher?approach, checking and double-checking
absolutely everything."
The Honeywell machine was completed in October 2003 and it has
been in production since then.
Further information on Honeywell is available at www.honeywell.com
|