THAT CAR EMBLEM IS ALMOST
CERTAINLY FROM POLYPLASTICS
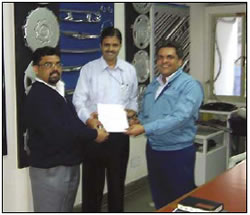 |
Kapil Gupta, Technical Director of Polyplastics (left) and Kamal
Gupta, Finance Director of the company (right) hand the purchase
order for the new machine to SR Chandrashekar, surrounded by
examples of the work they do for the automotive industry. |
Not many companies in the world can boast of holding 80% of the
market in which they operate, but that is the proud claim of Polyplastics,
a leading Indian manufacturer of automotive components and automobile
OEM supplier.
Amongst the markets in which they operate is the manufacture of
emblems and monograms ?the chrome-plated logo that sits on the
radiator grille and on the back of every car, electroplated grills
and rear number plate garnishes. Eighty out of every 100 cars in
India bears an emblem manufactured and plated at Polyplastics?plant
in Yamuna Nagar in the northern Indian state of Haryana (200 km
north of the capital city of New Delhi).
The company is a major supplier for Suzuki cars in India and back
in 1997 it entered into a technical collaboration with Sakae Riken
Kogyo Co. Ltd. of Japan for the manufacture of PVC extrusion door
mouldings and other car parts.
They also specialise in hubcaps and wheel covers, automotive plastic
moulded parts, auto-electrical assemblies, ABS electroplated automobile
components for decoration, aesthetic parts, car spares and accessories.
Yes, they know cars inside out!
Polyplastics has recently bought a very special automatic electroplating
line from PAL and Kamtress Automation Systems Pvt Ltd that, once
commissioned by the end of this year, will be used for plating on
plastic components for Suzuki, Honda, Ford, General Motors, Toyota
cars and perhaps many more world-renowned car-makers too. This plating
line will be set up with technical assistance from Sakae Riken Kogyo
Co. Ltd.
Like their emblems, this is a new automatic line that will really
stand out from the crowd! "It’s a complicated line with seven transporters
and cross transfer shuttles," explains SR Chandrashekar of Kamtress,
PAL’s Indian agent. "No other plastic component manufacturer in
India has an automatic line of this magnitude. In fact it’s a set
of two lines next to each other separated by a walkway. Each line
is approximately 47m in length and 3m high x 5m wide; and designed
to produce about 4000ft2 of plated plastic components per week."
Like many installations in India it is a clever combination of PAL’s
and Kamtress’s technology and design with some locally sourced components
to lower the capital investment.
"We are very much looking forward to the set-up of the new line
and its smooth running," explains Kapil Gupta the technical director
of Polyplastics. "There were several deciding factors when we came
to make our decision about who would supply our new equipment, finally
we narrowed it down to a PAL/Kamtress machine after assessing the
commitment of the PAL and Kamtress teams in executing the project
for us. Although the other quotes were more competitive, we were
confident to have banked on PAL and Kamtress due to their vast experience
in the field of metal coatings. Our decision to go with PAL and
Kamtress was strengthened after visiting the PAL plant in China
and some of their installations of similar plating lines. We were
convinced that we would be able to have a high uptime on their machines
in comparison to the other suppliers. We are now looking forward
to a long and lasting relationship."
Established in 1967, Polyplastics is now an ISO-9002/QS-9000 company
so the quality of work produced by the new PAL & Kamtress machine
is of vital importance. "Quality of work is something that we know
all our customers want, and we are able to give it to them time
after time on all our installations," says SR Chandrashekar.
A "time line" on the Polyplastics website shows the many milestones
they have passed over the last 37 years since the company was set
up with a small tool room for manufacturing special spacers for
coaxial telecommunication cables. Their expansion programme over
the years has not only seen them grow physically, but expand into
an impressive array of industries too ?including the textile, defence,
refrigerator and, of course, the automotive industry (in 1982);
as well as exporting telecomm components to Finland, Austria, Italy
and the UK.
"Our main strengths lie in the expertise developed through long
experience, constant innovations and adoption of the latest technologies
by a dynamic technical and managerial team supported by dedicated
work force," explains Mr Gupta. "Intelligence, creativity and skills
perfected over 37 years are now at the service of OEMs for sourcing
world-class components having highest quality."
Further information at www.polyplasticsindia.com
|