The Development of MCP-PAL
An exciting period resulting in the development of a machine that
offers tremendous
cost-effective advantages to the PCB industry
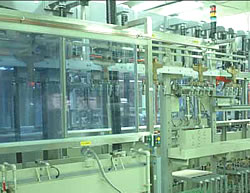
From scale model to real full size MCP-PAL machine |
PALs
Deputy Managing Director, Ronnie Wong explains the reasons behind
the exciting co-operation between PAL and Marunaka, which has produced
the new MCP-PAL (Marunaka Copper Plater) machine.
We were thrilled in the late 1990s with the development of our
PALTECH horizontal plating system, through which the first
panels successfully ran at Kintech, in March 2000. Headed by
Dr Paul Henington, much time and effort was spent by NewTech
engineers in its development and in further understanding its
performance and reliability. It was a measure of the creative
talent that resides in our factories in Hong Kong and our main
production plant at Shenzen, and its development and commercialisation
earned us a strong reputation for rising to challenges.
It was a wise man who said "timing is all"
and
of course,
PALTECH was deemed ready for our customers at just that
moment when the world went into something of an economic
downward spiral and the price of PCBs dropped with alarming
alacrity. Result? Most of our customers were faced with a need
to buy new machinery but the feeling was, that although our
horizontal system was indeed state-of-the-art, it was just too
expensive to buy in the belt tightening economy.
At the same time, the cry went up in Taiwan for a "surface
contact free" plating system for the production of fine line
circuitry. Something we knew that PALTECH could not cope with easily,
so we looked for a new solution.
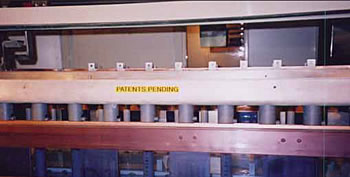
“Patents Pending?- the sign that says it all!
We have a very close working relationship with a great many of
our customers. Our machines are not "off the peg", we
work
with our engineers in customer companies in every instance to
build exactly the machine they want. This close relationship
leads to them sharing their aspirations and market intelligence
with us. Increasingly, they were telling us of a Japanese
development that they thought we should be looking at and
emulating the vertical continuous plating system.
Our Japanese agent, Ken Tamba, was extremely helpful. Together
we researched what was on the market in Japan. As a company,
we spent time considering whether we should develop the whole
system ourselves, or whether we should join forces with one of
the Japanese companies that our research had revealed was
working in this field.
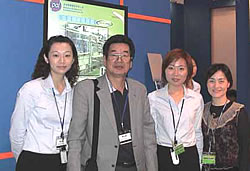
The President of Marunaka, Mr Masatsugu Nagakura visited
the stand at TPCA 2003 and is seen with some of the stand attendants
and in front of a poster about the MCP-PAL machine |
We
decided that the best route would be one of co-operation, and it
was at the end of 2001 that we signed a strategically important
agreement with Marunaka Kogyo Co Ltd. Their vertical continuous
plating system had been working since 1998 and over 30 lines had
been sold all of them in Japan. We were interested in their
technology; they wanted their machine to have worldwide exposure
and be developed to meet worldwide needs we had the ingredients
for a perfect co-operation agreement! Once the agreement had been
signed, we formed a special engineering team (now known as PALs
New Product Development Department) led by our Engineering Director,
Mr C.W. Wong. Members of the team visited Japan to gain a greater
understanding of the MCP machine, and we ended up with literally
thousands of drawings from Marunaka, all of which then had to be
translated at the Shenzhen plant.
Without the benefit of any confirmed orders we determined in
early 2002 to set about building the first test line in our Hong
Kong factory. Work on it began in April 2002 and was
completed by June that year. You can imagine the steep learning
curve we experienced we learned all about the qualities of
the
machine during the manufacturing process and our experience
gave us the confidence to plan to launch it into the market during
2002.
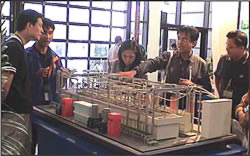
A scale model of the MCP-PAL was the star of the PAL/Pelsco
stand at TPCA 2003 - Patrick Chan, Asst Regional Manager for
the Taiwan market answers visitors?questions on the machine |
Getting
the test line built was just the start of things! We then spent
nine months running plating tests to confirm its performance and
do test runs to show potential customers what it could achieve several
Taiwan-based customers like Compeq, Kinsus, Unitech and Wus supported
the project strongly and prepared panels for us to use for testing.
They also sent their experienced engineers to our test line in Hong
Kong for performance verification and to suggest improvements.
NewTech, and especially Billy Ng, spent long periods working
on improving the plating quality and the machine itself. During
this period we added many PAL features to the machine
including Data Monitoring software and environmental
enclosures. Now, the MCP is capable of handling thin panels
right down to 0.06mm, micro via plating and via filling.
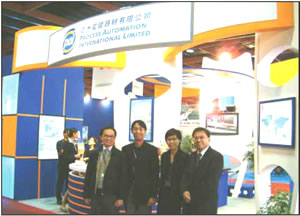
E B Ho, Ronnie Wong, Ada Yung and Oliver Leung - senior members
of the management teams of PAL and Pelsco - at TPCA 2003 |
So
far sales of our machines have been mainly in Taiwan and China,
but what a success story we have there to talk about! Since 2002
we have sold over 20 lines. The first was sold to Kinsus who now
have four MCP-PALs; Wus were our next customer they now have
five of the machines; the third and fourth lines went to Unitech
who now have four lines; and the fifth was ordered by Compeq who,
like Wus, have five. As can be seen by the number of machines that
each of those five companies now have, our customers were delighted
by the performance of their new machines and ordered again, and
again and again. In addition Tripod have two, and Nanya and Unimicron
each have one. A tremendous success story at a difficult financial
time for the industry!
We firmly believe that the MCP-PAL will help the PCB industry
to produce high quality PCBs cost effectively, thanks to low
capital investment, low running and maintenance costs. What
more could they possible want!
......AND FOCUSING ON ONE OF THOSE PURCHASERS
Kinsus Interconnect Technology Corporation is a relative
newcomer, having set up in Taiwan only in September 2000 with
their 144,000sq.ft facility completed in May 2001. Their U.S.
subsidiary, Kinsus Corp, based in California-San Jose was
incorporated in October 2000. They specialise in IC substrates
PBGA, CSP, Cavity Down BGA, and Flip Chip.
Since then they have been truly flying as a host of facts and
figures show
Capital expenditure to date US$58 m
2002 sales US$27.8m
2003 sales up to US$63.5m
2002 factory expansion to 270k sq.ft
2004 factory expansion to 500k sq.ft
2003 capacity 20kk for all their product mix
2004 predicted capacity 25kk
"The secret to our success is that, not only are we a manufacturing
service provider, but a technology service provider too,"
explains Jeff Chang. "We are great believers in being able
to
claim that we are a total solution provider on all types of
substrate; we are leaders in the technology field; we believe in
offering a quick turn around service and in continuously driving
advance product & low cost solution.
"We grab new technology with enthusiasm! Thats why we
enjoy
working with PAL, whose New Technology and New Product
Development Departments are continually looking for new ways
of helping their customers achieve their objectives. In a drive
to
achieve better plating uniformity, we tried out a horizontal
system. Its performance gave us acceptable results, but for a
variety of reasons, including our aim to constantly drive down
costs and our need to plate panels in excess of 20" meant that
we
felt the time was right to switch to vertical plating.
"We were delighted to hear of PALs work on the MCP-PAL
machine and eagerlyworked with PAL on its development,
preparing panels for them to use for tests; and sending engineers
to Hong Kong to keep in touch with progress and make
suggestions. We took delivery of our first MCP-PAL in October
2002, using this line for both pattern and panel plating, which
resulted in us making changes to the original design (not always
the best policy, as we found!). PAL improved the system for us
and since then we have placed orders for more machines to keep
in step with our rapid expansion, and desire to keep improving
our hi-end products on which it is essential that we achieve more
than 85 per cent plating uniformity for Microwave RF, thick
Copper uniformity is essential.
"The MCP-PAL lines are helping us achieve our objectives and
we are delighted with the results what more can we possibly
want! We have enjoyed this experience of working with PAL on
the continuous improvement of the MCP-PAL and look forward
to enjoying the results of their ongoing R&D work."
Further information on Kinsus from www.kinsus.com.tw
|